Sound quality case studies
Case Study 1
The Annoying Dishwasher: Sound Quality Doesn’t Always Mean Quieter!
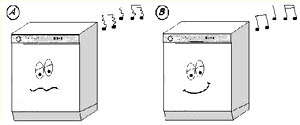
Poggenburg and Genuit [1] give the example of a dishwasher. A clear aim was identified: Reduce the sound power level to as low as possible, which would also mean that overall a quieter machine would be made. This led to the assumption that the preferred machine would be the machine currently with the lowest sound power level. Dishwasher A had a sound power level of 44.6dB(A) whereas dishwasher B had a sound power level of 47 dB(A), a difference of 2.4dB which shows that B has close to double of the noise power of A.
However sound quality testing revealed that machine B was in fact the machine with the preferred sound. Further analysis revealed that this was because machine A produced a ‘splash’ sound which was more annoying than machine B. Machine A also had a much lower sound power level therefore the more annoying ‘splash’ sound was not masked by the general operational sound of the machine. This led to the preference for machine B, which had a higher sound power level, and was louder, but had a less annoying sound. Furthermore, a reduction of sound power level would have led to a worsening rather than an improvement of the sound of machine A, because there would be even less noise to mask the annoying sound.
Case study 2
Vacuum cleaners: Cost Effective Sound Quality
In 1988 HS Sagoo’s PhD thesis [2] detailed a noise reduction project for vacuum cleaners, where the product sound was improved at a cost of 93.6p per vacuum cleaner. Prior to Sagoo’s work, noise consideration of the product had been given a low priority. It was discovered that vacuum cleaner design was not optimised from the point of view of noise emission. The designers’ lack of experience in noise reduction was cited as a reason for this, and therefore Sagoo highlighted the necessity for education in noise reduction techniques and developed guidelines for good acoustical design. An investigation of the principles of noise generation for each major source in a vacuum cleaner revealed that the three major areas of interest in terms of noise and vibration were:
Mechanical Noise sources
Sources from the electric motor included noise from bearings and/or from the rotor being ‘out of balance’. These sources were identified as being interrelated since any misbalance of the rotor will result in an additional load being placed on the bearings. Bearing noise was not identified as a major problem on a new product but could become a major problem later in the lifetime of a product. These noise sources could also result in additional structural vibration which in turn could lead to sound generated by the outer surface structure.
Electromagnetic sources
Vibrations caused by magnetic forces have been found to generate noise by transmitting vibrational energy to the outer casing of the motor. An effect which prompted Fujimoto (in 1983) to introduce a second motor which would counteract the vibrations of the first. The solution however is limited by cost.
Aerodynamic sources
The fan noise of the vacuum cleaner was found to generate both broad band noise as well as harmonic components. Harmonic noise relating to the frequency of the rotation of fan blades is what gives helicopters their distinctive sound. In the vacuum cleaner, it has been shown that this noise can be reduced by techniques such as the use of unevenly spaced blades to apply amplitude modulation to the tone and spread energy into the side bands. (It is also possible in some machines to change the frequency of the harmonics by changing the number of blades, blade size and speed of roatation, and therefore generate noise which is less audible). The main source of broad band noise is turbulence in the air flow. The interaction of turbulence with structures in the duct can also lead to the production of pure tones. Standing waves can be produced, or a sudden expansion or constriction within a duct can lead to oscillations which result in acoustic waves. Techniques such as using a sharp bend to change the attenuation at particular frequencies, adding an absorption treatment to the inside of the ducts or using circular ducts instead of rectangular ducts to change resonant frequencies, can all have important noise reduction effects if used appropriately. The addition of a silencer is another possible way to reduce unwanted sounds.
Noise source identification techniques such as the ‘sequential removal of components’ were applied. This is a technique where the noise levels and vibration of an appliance is recorded as it is systematically disassembled and then rebuilt removing constituent parts e.g the appliance housing or dust bag for a vacuum cleaner. This helped in the identification of the major sources of noise, thus allowing the application of noise reduction treatments in the most relevant areas. A resulting list of recommendations for good acoustical design practise included factors such as:
- Selection of a low speed motors over a high speed ones.
- Improving the lubrication of bearings.
- Maintaining closer design and manufacturing limits for bearings and moving parts.
- Avoiding a close gap between moving elements.
- Avoiding structural resonances.
- Reducing large flexible noise radiating areas into smaller areas which have lower radiation efficiency.
- Using linings of acoustically absorbant material.
- Taking advantage of directivity effects by directing inlet and discharge openings away from the direction of listeners.
- Minimising flow velocity through passages and bends.
- Avoiding abrupt changes in the cross section of ducts and bends to reduce turbulence.
- Placing all vibrating sources on a common sub-base which can then be isolation mounted.
- Avoiding rigid structural or flanking paths between isolated components.
It was concluded that it is not only important to consider noise control at the early stages of design but to study the whole of the manufacturing process for a successful noise reduction. Variations of the motor and cleaner quality during manufacture on the production line had to be taken into account to maintain sound quality standards right through from the earliest conception of a new product to the final stages of manufacture.